Finger Splice for single-ply conveyor belts
The strongest, most reliable splicing method for your conveyor belts
Discover rubber belt splicing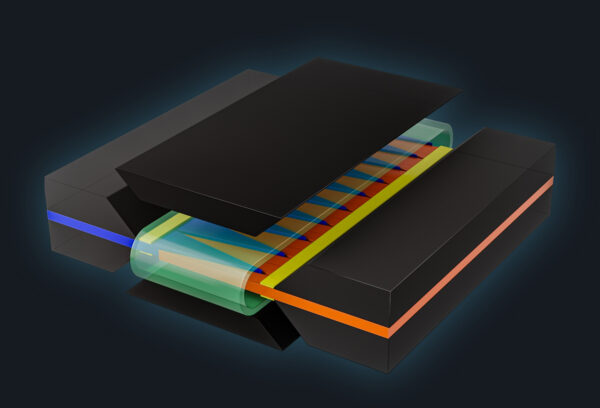
The weakest point
It is estimated that nearly 80% of unplanned conveyor stoppages are caused by splice joint problems.
The weakest point of any rubber conveyor belt is the splice joint. Because of the safety implications and the potential loss of output caused by splice joint failure, it is critically important to maximize the strength and long-term durability of the joint. The splice must withstand a wide range of changes in tension as well as other factors such as short transitions, “S” drive arrangements and impact from heavy materials falling from height on to the joint. Added to that is the dynamic stress caused by the continual flexing over drums and pulleys. Even though a great deal of time and care may have been taken in calculating the correct belt specification and buying a good quality conveyor belt, it can all be easily wasted if the splice joint proves to be unreliable.
The advantages of finger splicing
The most popular method of making a splice joint is the use of vulcanized splicing, which can be either a hot or cold splice. Within this, the two most common techniques used to create a vulcanized splice joint are the step splice and the finger splice. Regardless of the method used, it is not physically possible to join a belt without some loss of longitudinal tensile strength but in the case of the step splice, its biggest disadvantage is that the loss is so significant because it always creates a proportional loss of tensile strength equivalent to one ply. For example, a 3-ply step joint can only achieve a maximum longitudinal tensile strength of 67%. This effectively means that in a typical multi-ply belt containing three plies or more, at least one ply exists purely to compensate for loss of the longitudinal strength incurred by making a step splice joint.
To help achieve the best finger splice joints we supply a range of professional quality finger splicing tools including templates, edge bar sets and belt skiver sets as well as complete tool kits!
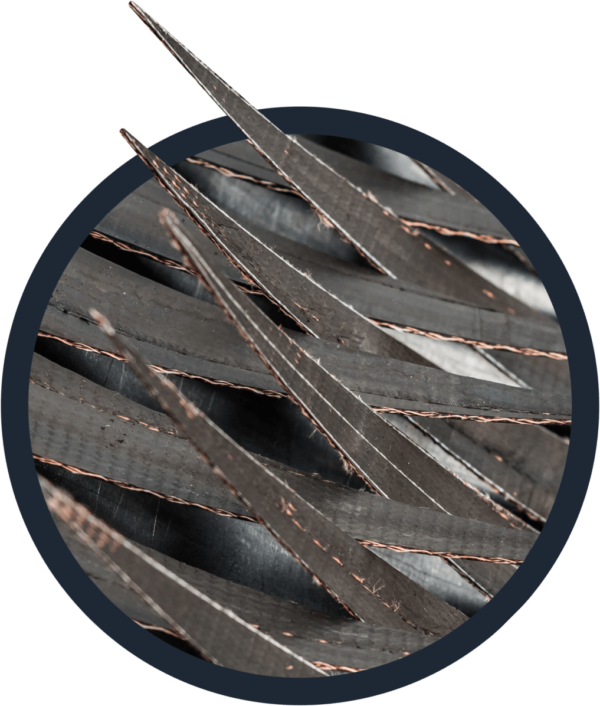
Finger Splice Testimonials
Real Stories
Maximize speed and accuracy
When preparing to make a finger splice it is a good practice to make use of dedicated templates with the finger shape predefined and ready to trace onto the belt. This helps to speed up the process and greatly improve accuracy. By comparison, templates are not available for stepped splices, so the accuracy depends much more on the skill and attention of the splicer who is measuring and cutting. The use of a template allows very accurate preparation and enables perfect alignment and matching and therefore the perfect splice between both belt ends.
Cost saver
Although step splice joints are generally easier and quicker to make compared to finger splices, the loss of longitudinal tensile strength must be taken into consideration when trying to establish the correct specification of belt for a specific conveyor. Therefore, the calculation should always include the safety in the splice at the given efficiency. The much higher retention of tensile strength provided by a finger splice means that it can often be possible to install a lower and therefore less expensive specification such as a 630/1 rather than an 800/4.
Finger splice for single-ply conveyor belts
Finger Splice + Single‑ply Technology = The Ultimate Solution
Single-ply conveyor belts are latest innovation in the belting industry. Thicker belt is not always stronger – that is a revolution for the belting industry. Single-ply belts offer many advantages compared to multi-ply belting.
- Far superior impact resistance
- Greater splice joint efficiency’
- Can be used on smaller than usual pulleys
- Low elongation, compared to ‘normal’ plied belting
- Good troughability
- Good running behaviour
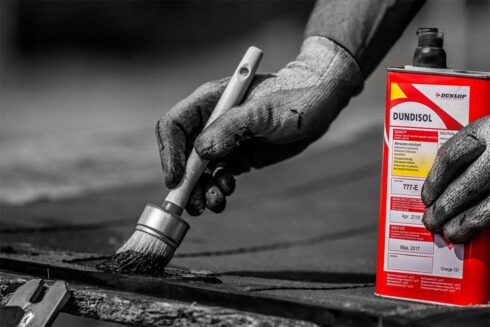